纤维增强水泥压力板生产线LOF水泥板生产线纤维水泥瓦生产线
发布时间 2024-06-27 11:28:40
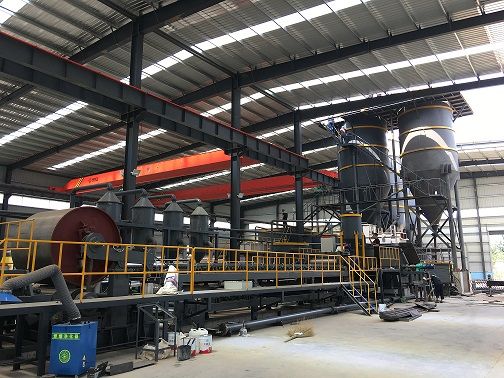
产品描述
材质 | 长度 2440㎜或可定制 |
---|---|
产品类别 | 纤维水泥板生产线设备 |
适用范围 | 防火绝缘 |
特殊功能 | 隔热隔音 |
颜色 | 自然水泥色 |
抗压强度 | 2.5-100 Mpa |
纤维水泥瓦或石棉瓦的制作离不开设备的运转,而纤维水泥瓦或石棉瓦生产线则是按照工序的步骤一步一步完成,今天我们就具体了解下石棉瓦生产线工序过程,让您对生产石棉瓦有所了解。
1、纤维水泥瓦或石棉瓦生产线的原材料储存
纤维水泥瓦石棉瓦所使用的原料进入生产现场所配备的仓库之中,以备于生产使用。石棉瓦原材料有石英粉、粉煤灰、水泥、石灰粉、石英砂、纸纤维、木纤维及其他纤维等。
2、纤维水泥瓦石棉瓦生产线的纤维处理
纤维水泥瓦石棉瓦生产所使用的增强纤维,经人工或机器机械化倒袋、抖袋、中间存料和向计量秤喂料。经计量秤自动计量好或者人工称重计量好的各种增强纤维,加入立式叶轮打浆机中进行充分松解,达规定时间后再加入一定量的硅灰石及砂光粉尘和其它掺加物,再进行充分松解拌合。
3、纤维水泥瓦石棉瓦生产线的纸浆处理
浆板纸加入立式高浓碎浆机中,加入定量水分松解,此过程间歇进行,每锅料需处理40-60分钟。经碎解后的纸浆经泵送入一级贮浆池。再加水稀释到较低浓度
进入两级双盘磨浆机逐级疏磨,以提高纸浆的打浆度。经疏磨后的纸浆送入二级贮浆池。如加工后纸浆质量不能满足生产工艺要求,必须进行二次疏磨,然后送入三
级贮浆池备用。为了方便计量处理好的成品纸浆,需要预先调节好纸浆的浓度,再通过容积计量法可以很方便地对纸浆进行计量。
4、纤维水泥瓦石棉瓦生产线的制浆工段
将松解好的纤维混合浆泵入打浆机,加入计量好的定量纸浆,再依次加入消石灰粉、石英粉、水泥等粉状物料。消石灰粉、石英粉、水泥分别从各自储库中通过螺旋
输送机送入电子秤计量后再下料或者人工称重下料。粉状物料加入后和纸浆及纤维混合浆在打浆机内充分拌合制得一定浓度的料浆,泵送至斗式储浆池中备用。
5、纤维水泥瓦石棉瓦生产线的储浆及预搅拌
制好的料浆在储浆池中储存,并定量均匀地供给单盘磨浆机,料浆经过磨浆机匀磨处理,达到进一步松解纤维及拌合料浆的作用。磨好的料浆进入预搅拌罐内搅拌,
预搅拌罐设称重浓度测量显示系统,可以检测出料浆的浓度并可人工进行调节。稳定的料浆浓度可以保证制板的稳定,可以方便地调节板厚。
6、纤维水泥瓦石棉瓦生产线的制板、接坯及堆垛
抄取制板工艺料耗低,生产稳定容易控制。料浆通过网箱过滤均匀挂在运行的工业毛毯上,并通过真空抽吸滤水,制板机成型筒将毛布上连续均匀的薄料层卷到成型筒上,达到一定厚度后,由厚度控制系统自动控制,成型筒上切刀将坯体切断,由接坯机将坯体铺开形成一张板坯,板坯在接坯机上运行时完成纵切并切除两侧料
边,经过三工位堆垛机时进行堆垛。堆垛采取一张钢模一张板坯方式,充分保证板坯平整。制板、接坯、堆垛全过程采用可编程控制器自动控制,自动化程度较高。
7、纤维水泥瓦石棉瓦生产线的预养护和脱模
湿坯堆垛后需经一段时间的预养护,使板坯达到初期强度,以利于机械脱模码垛或者人工脱模。亦可设立预养护设有预养窑,一般温度保持在50~70℃,4h~6h即可出窑。预养窑壁设散热管,依靠蒸汽提供热源。
8、纤维水泥瓦石棉瓦生产线的蒸压养护
如果想尽快达到大量商业销售目的,可设立蒸压养护工段,经过预养护的石棉瓦板坯进入蒸养釜内进行高温蒸压养护,使板坯增加粘合性,使其抗折强度增加。
9、纤维水泥瓦石棉瓦生产线的烘干磨边
经过蒸养釜养护后的石棉瓦通过烘干机的烘干,使板材的水分去除,并进行四角磨边倒角机进行磨边打磨,或者人工打磨,直至符合出厂需求。
由于纤维水泥瓦或石棉瓦具有轻质、高强、防火、保温隔热性能的良好性能,是新型环保的建材,符合各种建筑行业的需求,因此产品的市场潜力巨大。以上就是纤维水泥瓦或石棉瓦生产线的全部工序过程
The production of fiber cement tile or asbestos tile is inseparable from the operation of the equipment, and the fiber cement tile or asbestos tile production line is completed step by step in accordance with the steps of the process. Watt understands something.
1. Raw material storage of fiber cement tile or asbestos tile production line
The raw materials used in fiber cement tiles and asbestos tiles enter the warehouse equipped on the production site for production use. The raw materials of asbestos tiles include quartz powder, fly ash, cement, lime powder, quartz sand, paper fiber, wood fiber and other fibers.
2. Fiber treatment of fiber cement tile asbestos tile production line
The reinforcing fibers used in the production of fiber cement tiles and asbestos tiles are manually or mechanically mechanized by pouring, shaking, intermediate storage and feeding to a weighing scale. Various reinforcing fibers that have been automatically measured by a weighing scale or manually weighed and measured are added to the vertical impeller beater to fully loosen, and after the specified time, add a certain amount of wollastonite, sanding dust and other admixtures The material, and then fully loosen and mix.
3. Pulp treatment of fiber cement tile asbestos tile production line
Pulp board paper is added to a vertical high-consistency pulper, and a quantitative amount of water is added to loosen it. This process is carried out intermittently, and each pot material needs to be processed for 40-60 minutes. The crushed pulp is pumped into the primary storage tank. Then add water to dilute it to a lower concentration and enter the two-stage double-disc refiner to grind step by step to improve the beating degree of the pulp. The thinned pulp is sent to the secondary pulp storage tank. If the quality of the processed pulp cannot meet the requirements of the production process, it must be ground for a second time, and then sent to the third-stage pulp storage tank for standby. In order to facilitate the measurement of the processed finished pulp, the concentration of the pulp needs to be adjusted in advance, and then the pulp can be easily measured by the volumetric metering method.
4. The pulping section of the fiber cement tile asbestos tile production line
The loosened fiber mixed slurry is pumped into the beating machine, the measured quantitative pulp is added, and then powdered materials such as slaked lime powder, quartz powder, and cement are added in sequence. The slaked lime powder, quartz powder, and cement are respectively sent from their respective storage warehouses to the electronic scale through a screw conveyor for measurement and then blanked or manually weighed and blanked. After the powdery material is added, the pulp and fiber mixed pulp are fully mixed in the beater to obtain a certain concentration of slurry, which is pumped to the bucket-type slurry storage tank for standby.
5. Storage and pre-mixing of fiber cement tile asbestos tile production line
The prepared slurry is stored in a slurry storage tank and is evenly supplied to a single-disc refiner in a quantitative and uniform manner. The slurry is homogenized by the refiner to further loosen the fiber and mix the slurry. The ground slurry is stirred in the pre-mixing tank. The pre-mixing tank is equipped with a weighing concentration measurement and display system, which can detect the concentration of the slurry and adjust it manually. The stable slurry concentration can ensure the stability of the plate making, and the plate thickness can be easily adjusted.
6. Board making, blank connection and stacking of fiber cement tile asbestos tile production line
The material consumption of the board making process is low, and the production is stable and easy to control. The slurry is evenly hung on the running industrial blanket through the net box filtration, and the water is sucked and filtered by the vacuum. The forming cylinder of the plate making machine rolls a continuous and uniform thin layer of the wool onto the forming cylinder. After reaching a certain thickness, the thickness The control system automatically controls, the cutting knife on the forming cylinder cuts the blank, and the blank splicing machine spreads the blank to form a slab. When the slab is running on the blank splicing machine, the slitting is completed and the edges on both sides are cut off. Stacking is carried out when the station stacker is used. One steel mold and one slab are used for stacking to fully ensure the flatness of the slabs. The whole process of plate making, blank receiving and stacking is automatically controlled by a programmable controller, which has a high degree of automation.
7. Pre-curing and demoulding of fiber cement tile asbestos tile production line
After stacking the wet billets, a period of pre-curing is required to make the slabs reach the initial strength to facilitate mechanical demolding and stacking or manual demolding. Pre-curing can also be set up with a pre-curing kiln, generally the temperature is maintained at 50 ~ 70 ℃, 4h ~ 6h can be out of the kiln. The wall of the pre-curing kiln is equipped with radiating pipes, which rely on steam to provide the heat source.
8. Autoclave curing of fiber cement tile asbestos tile production line
If you want to achieve a large number of commercial sales as soon as possible, you can set up an autoclaved curing section, and the pre-cured asbestos tile slab enters the autoclave for high-temperature autoclave curing to increase the adhesion of the slab and increase its flexural strength.
9. Drying and edging of fiber cement tile asbestos tile production line
The asbestos tile cured by the steam curing kettle is dried by a dryer to remove the moisture of the board, and then be polished by a four-corner edging chamfering machine, or manually polished until it meets the requirements of the factory.
Because fiber cement tiles or asbestos tiles have good properties of light weight, high strength, fire resistance, heat preservation and heat insulation, they are new environmentally friendly building materials and meet the needs of various construction industries, so the product has a huge market potential. The above is the whole process of the fiber cement tile or asbestos tile production linezzxlyjx.comWhatsApp15324995777
联系人 | 孙经理 |
---|---|
联系电话 | 0371-60326788 15324995777 |
地址 | 河南省郑州市巩义市兴华街6号 |
邮箱 | 2379722930@qq.com |