陶粒生产线,陶粒设备,陶粒生产设备,陶粒制作设备
发布时间 2024-02-25 19:37:37
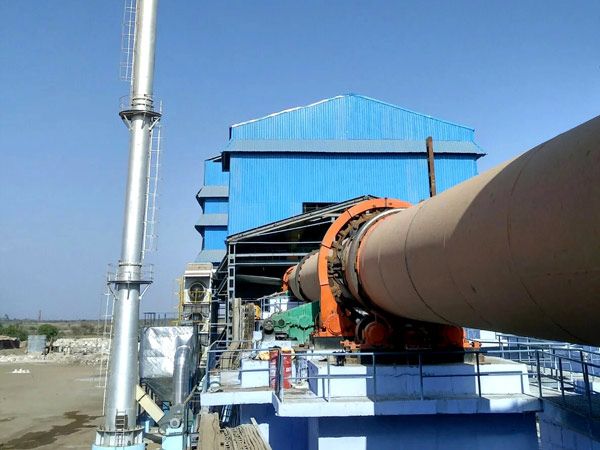
产品描述
陶粒生产线生产陶粒的主体设备主要包括:制粒机、筛选机、主窑体、喷煤系统、控制柜等。其中原料仓下部的喂料器、窑体转速和拱煤量均为无级调速,以便调整其工艺参数,在保证产品质量的前提下获得**大的产量。该套陶粒设备具有产量高、连续生产、产品活性大、成品质量高、节能环保、燃料能耗小、燃料使用要求宽松等优点。
在陶粒生产线中用到的陶粒设备有颚式破碎机、锤式破碎机、球磨机、回转窑等。整个工艺流程包括破碎、配料、粉磨、制球、煅烧、煤粉制备、成品冷却、筛分、包装等工序。
陶粒砂设备工作原理:即窑体的预热段和干燥段可单独控制其转速,以便根据原料的状态控制其预热时间。黏土陶粒近年来由于受到土地资源的限制,在某些地区已被禁止生产和使用。但有些地区可以利用河道淤泥、废弃山土等进行生产。
陶粒生产设备回转窑是煅烧陶粒原料的**回转窑,是陶粒的**设备,陶粒回转窑广泛适于污泥、黏土、黄泥、河底淤泥、粉煤灰、页岩、炉渣、等各种物料陶粒的煅烧与锚点制作。也是陶粒生产线中很重要的一个设备,具有单位体积高,窑炉寿命长,运转率高,操作稳定,传热效率高,热耗低等特点,是理想的陶粒煅烧设备。陶粒回转窑工作原理与其它回转窑类似,窑体与水平呈一定的斜度,整个窑体由托轮装置支承,并有控制窑体上下窜动的挡轮装置。传动部分除设置主传动外,还设置了为保证在主传动电源中断时仍能使窑体慢速转动、防止窑体变形的辅助传动装置。窑头采用壳罩式密封,回转窑尾装有轴向接触式密封装置,保证了密封的可靠性。陶粒回转窑一方面是燃烧设备,煤粉在其窑中燃烧产生热量;同时也是传热设备,原料吸收气体的热量进行煅烧。另外有时输送设备,将原料从进料端输送到出料端。而燃料燃烧、传热及原料运动三者间必须合理配合,才能使燃料燃烧所产生的热量能在原料通过陶粒回转窑旋窑的时间内及时传给原料,以达致到高产、优质、低消耗的目的。
原料(粉煤灰+定量的外加剂)混磨 — 制粒 — 烧胀 —堆放 — 运输(装袋)生产粉煤灰陶粒宜采用双筒回转窑,即窑体的预热段和干燥段可单独控制其转速,以便根据原料的状态控制其预热时间。黏土陶粒近年来由于受到土地资源的限制,在某些地区已被禁止生产和使用。但有些地区可以利用河道淤泥、废弃山土等进行生产。陶粒设备工艺过程为原料搅拌 —制粒— 筛选— 烧结 —堆放— 运输(装袋)在操作中应注意了望,防止物料在窑内结团而影响质量。
年产20万立方米的轻质陶料生产线的焙烧主机设备选用双筒回转窑+竖式冷却机组成烧成系统。技术方案介绍:
陶粒生产设备(以回转窑煅烧轻质陶料为例)需要根据原料,燃料的种类不同,采取相应的预处理措施,在原料的储存、破碎、筛分、配料、均化、搅拌、成型、煅烧、冷却、成品输送及筛分以及窑头及窑尾的废气处理等工序,均需要根据物料的性质、粉尘量的大小选用适宜的收尘设施,目前对于粉尘的处理,大多采用袋收尘器处理,可有效降低含尘气体中的固体颗粒物的粉尘浓度,按照GB4915-2013《水泥工业大气污染物排放标准》规定,除烘干机、烘干磨、煤磨、冷却机及窑头、窑尾收尘系统粉尘排放浓度为≤30mg/Nm3外,其余各扬尘点的收尘器出口粉尘排放浓度均≤20mg/Nm3。
原料配料及输送
储存在预均化堆棚内的河泥、单独储存的污泥分别通过装载机倒入各自的配料料仓,通过配料料仓下的螺旋闸及螺旋计量装置后送入双轴搅拌机进行搅拌,**后通过皮带输送机输送至窑尾烟室入窑。
窑尾废气处理系统-APC
出回转窑的废气进入窑尾换热器、反应塔、袋收尘器进行处理,达到排放标准的废气经窑尾废气风机排入大气。
反应塔和袋式收尘器的积灰经螺旋输送机、提升机送入窑灰仓,再经过窑灰仓下的卸料计量装置及螺旋输送机送入双齿辊破碎机进行混合和破碎。袋式收尘器内的积灰也可经中间小仓、手动螺旋闸、计量装置、气力输送装置输送至反应塔进行进一步反应。
反应塔内设喷水装置,外部设置水箱,必要时开启,经管道输送至反应塔进行增湿降温。
反应塔旁设置活性炭粉仓和活性石灰粉仓(Ca(OH)2),活性炭粉和活性石灰粉分别经手动螺旋闸、计量装置、气力输送装置送至反应塔进行反应,除去窑尾废气中的有害物质。
为保证APC系统的正常启用,在窑系统开机前,设置有循环风加热系统预热APC袋收尘器及反应塔,窑系统正常启动后停用此循环风加热系统。
通过APC系统的废气实现了以下三个主要功能:
袋式收尘器-.除去废气中的固体颗粒物,使粉尘浓度达标排放;
活性石灰-除去废气中的SO2,HCl,HF,NO,NO2等酸性有害物质;
活性碳-除去废气中的镉、汞、铅、砷、铬、铜、锌、镍等有害重金属及二恶英。
在出窑废气管道上及窑尾废气烟囟上分别设置气体分析仪各一套,用于检测窑尾废气处理前后的有害物质含量,根据污染物的排放检测浓度值分别调整活性碳及活性石灰的加入量,达到达标排放要求。
经螺旋输送机送来的原料进入双筒回转窑进行烘干、成球和煅烧。这一过程是在由低转速的干燥窑和快转速煅烧窑所组成的双筒回转窑内进行的。泥饼进干燥窑后,与热气体作反向运动,在窑内多种热交换器及特种装置作用下,边干燥边成球,成球的颗料在窑内煅烧后进入竖式冷却器进行冷却。
.窑头、陶粒冷却及输送
窑头燃烧器可适用于天然气或煤粉以及木屑等,具体情况根据当地条件确定后进行选择。
燃料经燃烧器及一次风机送入窑内煅烧,落入竖式冷却机的陶粒被鼓风机鼓入的冷空气冷却,出窑陶粒落入立筒冷却机的四个冷却室,冷却后的陶粒经4台电磁振动给料机卸料,卸出的陶料通过链斗输送机输送至陶粒成品库库顶进行分级。
陶粒分级、储存及装车
经链斗输送机送来的陶粒进入多层筛进行筛分,筛分后的各级配颗料的陶粒分别储存在各自的储存库内,设有3个储存库分别储存0-3,3-10,>10mm的陶粒,陶粒经储存库下的汽车散装机装车后运输出厂。
空压机站
全厂设置二台空压机,用于满足全厂收尘器、阀门等用气的需要。
煤粉制备及输送(可选)
储存在原煤堆棚内的原煤经装载机、提升机输送至原煤仓,原煤仓内的原煤经计量后输送至煤磨,原煤经烘干粉磨后进入煤磨袋收尘器进行收集,收集下来的煤粉进入煤粉仓,通过煤粉仓底的计量装置后,煤粉经罗茨风机送至窑头燃烧器进行燃烧。经收尘器处理后的气体排入大气。
天燃气阀组(可选)
若需要使用天然气,需在燃烧器前设计天然气阀组一套进行天然气的处理,以满足燃烧器进气及安全生产的需要。
生产效果说明
a.粉尘排入浓度≤30mg/Nm3;
b.烟气经处理后达标排放,满足《生活垃圾焚烧污染控制标准》(GB48485-2010)的要求;
c.污泥处理能力200TPD(80%水分);
d.陶粒生产能力600m3/d,年产轻质陶粒20万m3;
e.热耗≤1000kcal/kg(陶粒);
窑尾废气余热的利用
据有关资料对我国页岩陶粒厂和粘土陶粒厂的窑尾烟气温度的测定,一般在450~550℃之间,窑尾烟气带走的热损失大于窑筒体表面的散热损失,占热耗总比例的21.8%,影响较大。目前对窑尾废气余热的主要利用方式是增设热交换器,若采用窑内造粒的双筒回转窑,可在窑尾预热带部位加装十字架式热交换器或链环式热交换器;也可在窑尾烟室的烟气出口管道后增设热交换器用于降低窑尾废气温度,并可将经废气加热后的热风收集利用于成型后陶粒生料球的加热,以回收余热,降低陶粒的废气热损失。
陶粒生产设备、陶粒设备厂家产品优势
1、结构简单,具有单位体积高,窑炉寿命长,运转率高,操作稳定,传热效率高,热耗低等;
2、温度自动控制、超温报警,二次进风余热利用,窑衬寿命长;
3、先进的窑头窑尾密封技术及装置,运行稳定、产量高等显著特点;
4、能耗低、产品经脱水、脱碳增白,性能稳定性好。
5、 这套设备经多方实践验证,是一套技术成熟,严谨的陶粒回转窑设备,在国内使用广泛!
陶粒的用途:
1、
陶粒具有优异的性能,如密度低、筒压强度高、孔隙率高,软化系数高、抗冻性良好、抗碱集料反应性优异等。特别由于陶粒密度小,内部多孔,形态、成分较均一,且具一定强度和坚固性,因而具有质轻,耐腐蚀,抗冻,抗震和良好的隔绝性等多功能特点。
2、利用陶粒这些优异的性能,可以将它广泛应用与建材、园艺、食品饮料、耐火保温材料、化工、石油等部门,应用领域越来越广,还在继续扩大。在陶粒发明和生产之初,它主要用于建材领域,由于技术的不断发展和人们对陶粒性能的认识更加深入,陶粒的应用早已超过建材这一传统范围,不断扩大它的应用新领域。
3、现在陶粒在建材方面的应用,已经由100%下降到80%,在其他方面的应用,已占20%。随着陶粒新用途的不断开发,它在其他方面的比例将会逐渐增大,建材、园艺、食品饮料、耐火保温材料、化工、石油等部门,应用领域越来越广泛。
我公司是中原地区专业的陶粒机械生产厂家,生产的系列设备广泛应用在各种选矿、破碎、制砂生产线当中。其中大型球磨机、陶粒砂旋窑、烘干机在国内具有较高的权威性。整套陶粒生产线,陶粒设备生产厂家,陶粒生产设备多少钱,我公司会根据客户实际需求提供全方位的价格指导与方案设计。
43
58
34
61
57
66
48
56